Welcome to our FAQs.
This section is updated regularly.
Designing using steel framing
Building using steel frames
Living in a steel framed house
The history of steel framing
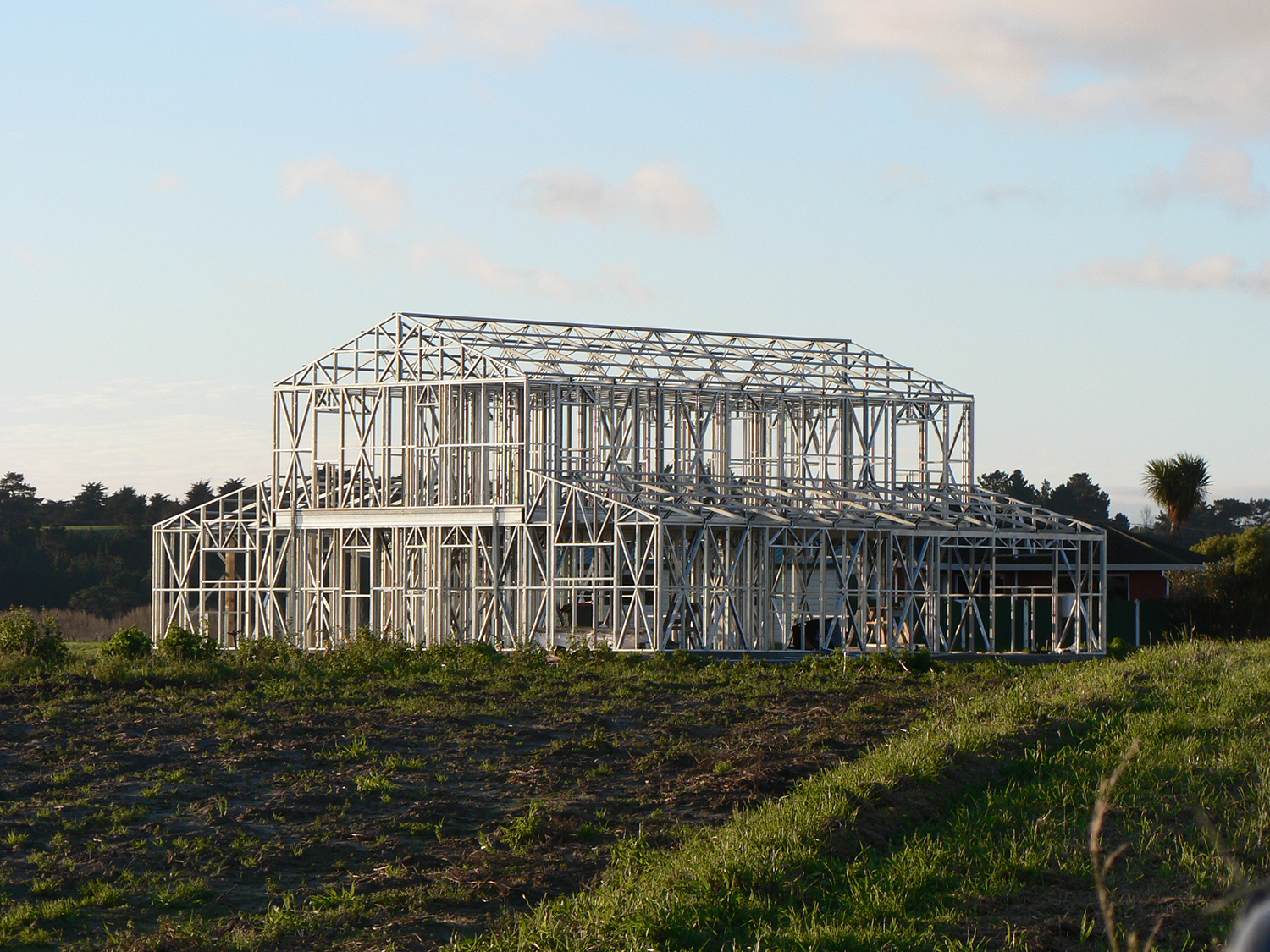
Designing using steel framing
All
Slabs
Fire
Noise
Timber
-
Is it true that the weight of a steel frame is only one third that of timber?
Yes, that’s roughly correct. All New Zealand steel framing is made from thin gauge, high tensile steel, meaning that the frames are approximately a 1/3 of the weight of comparable timber framing.
-
What is the difference in cost between timber and steel framing?
This naturally varies with the volume purchased and the design adopted. However, generally, steel is similar in cost to timber – the final constructed cost will be the same or less for a house of comparable size and quality. Although framing costs are only around 10% of the total building cost, steel provides other cost advantages too. As it is a lot faster to erect and frames are much easier to handle there are usually no call-backs or cracking to plaster linings, which reduces labour costs.
-
Can I convert plans from timber to steel?
Absolutely. You will need to apply for a variation to a building consent – click here to find out more. Your engineer will need to re-design construction loads, hold-downs, and brackets. Your architect / designer will also need to amend drawings / specifications to include a thermal break and review energy efficiency (H1) calculations.
-
Steel framing needs a thermal break to address potential for condensation to form on steel framing, while timber doesn’t. So, is timber framing better than steel?
The reason steel needs a thermal break is because of its high heat conductivity. Without the thermal break it means that when the inside of an external wall is warm compared with the outside, sufficient heat will flow through the steel stud to cool the inside surface of the wall, causing condensation and compromising the wall’s insulation rating.
This conductivity is often portrayed as being a weakness with steel. However, it is one of its greatest strengths. It means that when the thermal break is in place, all the steelwork on the inside of the thermal break remains above the temperature at which condensation from moisture in the wall cavity will occur – which ensures long term durability of the stud.
The outside of the timber stud will attract condensation during winter and, with the resulting increase in moisture content, movement that damages linings and potential long-term durability problems. This occurs in timber irrespective of the weather tightness of the external cladding.
-
Has Cold Formed Steel got a fire rating? What happens in a fire?
Neither light steel framed construction nor light timber framed construction have a fire rating in themselves – both require the application of fire-resistant linings. When these are applied both can deliver whatever magnitude of fire resistance is required.
Regarding performance of houses in fire, CFS has two very significant advantages over light timber framed construction. The first is that it is non-combustible. When fire burns through the linings it will not spread within the framing cavity in steel framing (whereas this is a major cause of hidden fire spread in timber framing). Electrical faults are the most common causes of fires in wall cavities – however these cannot ignite a steel frame.
The second big advantage is that it does not increase the fire load. There is at least 20 kg of timber per square metre of floor area in a timber framed house. This is 75% of the design fire load of a house contents, which means that a timber framed house is carrying at least 1.75 times the fire load of a steel framed house. The higher the fire load, the more severe the fire.
Given these two advantages it is not surprising that fire case histories show steel houses perform very well in house fires, with little or no damage to the framing structure. Indeed, if steel framed members are not visibly distorted, they can be left in place, cleaned and, if necessary, recoated.
-
How well does steel framing stand up to earthquakes or hurricanes?
CFS can be engineered to meet the highest seismic and wind loads prescribed by the NZ Building Code. Steel has the highest strength to weight ratio of any framing materials. A lighter structure with stronger connections results in lower damage from earthquakes. Steel framed houses in Christchurch suffered superficial but no structural damage during the recent earthquakes. Using stronger connections (i.e. screws over nails) can further assist house to withstand greater winds, including cyclones.
-
Can I use brick veneer with steel framing?
Yes, you can. Most steel framing construction in New Zealand uses brick veneer as a cladding because, like the steel frame behind it, this veneer lasts a very long time. New Zealand CFS has been seismically tested at Swinburne University in Melbourne to many more times the seismic forces than we ever have had in New Zealand. There was no damage to the structural frames and only minor dislodgement of bricks due to the great flexibility and strength of CFS.
-
Can I have my home designed by a steel frame supplier?
Yes, some steel frame suppliers provide design services. However, NASH encourages the use of architectural designers who are members of ADNZ or architects who are members of NZIA.
-
Aren’t steel frames noisier than timber?
No – steel homes are quiet inside. The exterior walls and ceiling are filled with thick insulation, restricting outside noise. Wood contracts as it dries and at ambient temperatures it expands. However, a steel framed home doesn’t creak, as humidity variations and temperature changes have less effect.
A steel frame is mechanically jointed. In a well-constructed and insulated home, thermally induced movement is not an issue. Steel framing expands and contracts at rates very similar to the other materials used in building, which means it is unlikely that there will be noise or cornice cracking problems. If a dark colour profiled metal roof cladding is chosen it is good practice to use an insulating separator between the metal cladding and the purlin, and to tell the roofer to use oversized holes.
-
How many storeys can a CFS building go up to?
NASH Standard Part 2 2019 is cited as an Acceptable Solution to NZ Building Code (B1, B2) for up to two stories. Currently there are engineered design solutions for up to 3 stories, depending upon location and ground conditions. Talk to your engineer or contact us if you have any questions.
-
What is the maximum span for a steel truss?
Normal CFS sections can be made to suit most residential spans. However, if high strength steel is used (due to its high strength to weight ratio), trusses can span larger distances.
-
Do steel framed homes have to be built on piles or concrete slabs?
Either will work. Steel frames can be fixed to a concrete slab or fixed to a lightweight steel floor system on concrete or steel piles. Lightweight steel flooring systems are ideal for elevated or sloping sites as they can minimise foundation requirements.
-
I want to design a penthouse on top of an existing six-storey office block in the CBD but there are weight and fire requirements for the site. Is steel suitable?
Steel is definitely the best choice for framing for many reasons, not the least of which is the ease with which frames can be hoisted up without the use of cranes. If site access is severely restricted frames can be assembled on the roof. Working with steel is also not so weather dependent as it is with other materials, and CFS also means lighter foundations. There are some excellent examples of this type of construction in the Auckland Central Business District.
-
My architect has designed our new home in timber. Can I convert the architect’s plan from wood framing to steel framing?
Most steel frames are made to the same dimensions as standard timber dimensions, so there is no problem in converting your plans to steel. Sometimes the biggest challenge is the architect, who has perhaps never worked with steel (don’t worry – once converted they usually become a fan).
-
What about steel floors in a two-storey building?
Because there are no issues with moisture, a steel joist floor system avoids swelling or shrinking problems associated with timber framing and floors. A viable alternative is to use a metal deck concrete floor in conjunction with steel joists. The strength and dimensional stability of steel framing lends itself to suspended concrete floors typically cast onto profiled steel decking. These floors offer thermal mass, good airborne sound insulation, and better impact sound insulation than most processed timber product floors.
Building using steel frames
All
Pipe
Lining
Rust
Cladding
-
How do I attach lining to the frame?
Plasterboard linings are screwed either horizontally or vertically into the steel frame using self-drilling screws and a suitable wallboard adhesive. The correct board should be used where either a sound or fire rating is required.
-
Do copper pipes have to be isolated from the steel frame?
Copper must be isolated because in the presence of moisture they will develop bi-metallic corrosion that could damage the protective zinc coating of the steel frames. The recommended method is isolation by using a plastic grommets.
-
Are the frames protected against rust at cut edges and drill holes?
Steel frames are zinc coated or galvanised, which protects steel from cut-edge corrosion by cathodic or galvanic action. Where the underlying steel base becomes exposed at cut edges holes or mechanically damaged areas, the zinc coating will corrode in preference to the steel.
The ability of a hot-dipped zinc coating on steel to protect it against corrosion is known as sacrificial, or cathodic protection because the cathode metal is the one protected. In this way the zinc coating adjacent to the edge or hole protects the cut area. Furthermore, because corrosion is a surface phenomenon, the cut surface protects the steel inside from corrosion. Rust cannot spread through steel from a point on the surface or cut edge –unlike rot in surface treated timber in which all cut ends need application of a rot-preventing chemical to preserve the durability of the stud.
-
Are more trade skills required to work with steel framing?
No. The skills required for building and finishing with steel frames are the same as they are with timber. Some trades may require additional specific information, which is provided by NASH or the steel frame manufacturers.
Steel framing is now an integral part of apprentice carpenter training, ensuring the next generation will be trained from the start of their careers in both materials. Builders that have worked with timber all their lives and changed to steel framing have been surprised how easy it is to work with steel.
-
How does steel framing perform as a support for wall lining materials and plaster cornices?
As screws and adhesives are used to fix linings there is no frame shrinkage with steel and so there is no cracking and nail popping of linings. Quite simply, lining materials in steel framed houses can be expected to perform better and look better than in houses built from timber.
-
How is electric cabling and telephone and computer wiring run in steel framed buildings?
The studs have pre-punched holes to facilitate easy cable installation, and grommets are fitted to protect the cable insulation when pulling them through the hole. Additional holes can be drilled or punched as required.
-
Will a steel frame rust?
No, not in normal use. Steel framing used in New Zealand is galvanised and, as framing is used in a “closed” environment, it is not normally subject to severe corrosion from marine salts or industrial pollution. Details are given in the durability statements from New Zealand Steel that support the AXXIS® framing.
-
How are different external claddings fixed?
NASH Building Envelope Solution 2019 is intended to be referenced as an Acceptable Solution to the New Zealand Building Code (NZBC) clause E2 External moisture. The Standard sets out solutions for the exterior weathertight envelope for steel-frame buildings constructed in accordance with NASH Standard Part 2.
Cladding solutions detailed in this Standard include the following: masonry veneer, stucco, timber weatherboards, fibre cement weatherboards, profiled metal wall cladding, fibre cement sheet, plywood sheet and EIFS
-
Is building with steel framing going to be quicker than timber?
Steel framing is lighter in weight so can be rapidly and simply assembled with fewer installers on a project. It is estimated that using steel framing is 30% quicker when compared with other building materials.
-
How can architraves and skirtings be fixed to steel frames?
Needlepoint self-drilling screws provide a simple fastening solution to CFS frames which, unlike nails, will never spring out. A combination of screws and adhesive can be used for timber while plastic skirtings can be secret fixed with clips.
Living in a steel framed house
-
How are different external claddings fixed?
NASH Building Envelope Solution 2019 is intended to be referenced as an Acceptable Solution to the New Zealand Building Code (NZBC) clause E2 External moisture. The Standard sets out solutions for the exterior weathertight envelope for steel-frame buildings constructed in accordance with NASH Standard Part 2.
Cladding solutions detailed in this Standard include the following: masonry veneer, stucco, timber weatherboards, fibre cement weatherboards, profiled metal wall cladding, fibre cement sheet, plywood sheet and EIFS
-
Can I hang a picture on the wall of a steel framed home?
Yes, provided it is correctly done. You can hang a picture of up to 10kg directly in the wall board using a fastener or a toggle bolt. Heavier objects (such as shelving, or a TV,) must be fixed through to the metal studs. These can be found using a magnet or by tapping, with the spacing normally being at 600mm centimetres. It is best to use a metal angle or bracket between two studs. Do not pre-drill the hole but instead use a type 17 drilling screw.
-
What type of barrier should be used in between the steel frame and treated timber?
For H1 treated timber normal building paper will act as a separator and will suffice if the area is closed. If the situation is sheltered or exposed with H3 timber then a more substantial separator should be used, such as window tape. This separation is more important if the site is ranked severe or very severe marine. If the frame is not clad, then an additional paint coat is necessary.
NASH provides guidance on barriers to use in all applications of steel framing and there is a clear and reliable New Zealand standard on which this information is based.
-
Will I be able to renovate my steel frame home?
Yes. Since steel framing allows for larger spans, the house can be designed without interior load- bearing partitions, making it easier for homeowners to do alterations without affecting the rest of the structure.
-
How do I fix the steel-frame to an existing timber frame when doing a renovation?
When attaching a steel frame to a timber one from the timber side, drill a clearance hole through the timber and screw a long self-drilling screw into the steel. If you are fixing from the steel side, use a 12# x 40mm type 17 screw.
-
Will vibration loosen the screws or rivets?
No. All steel frames are designed and braced to resist wind and earthquake stresses and the number of fasteners is more than adequate to rigidly hold the house frame together. Because the steel is dimensionally stable screws and rivets don’t work loose over time either (as can happen with timber).
-
Does lightning affect a steel-framed home more? Is steel framing dangerous when lightning strikes?
No. The frame offers better protection than other construction materials because, as steel creates a positive earth, it is a good conductor. This means that the electrical energy of lightning is conducted straight to the ground. As all steel frames are required to be earthed, lightning has less effect than framing made with other materials.
-
Can a steel frame house still be energy efficient?
Steel framing must meet NZBC energy standards (and can easily meet higher standards too). Also, because it is straight and true, the framing helps prevents cracks due to shrinking or warping, thus preventing air leaks that result in loss of energy. A key component in this is the thermal break which has other significant advantages as mentioned earlier. This thermal break interrupts the thermal bridge between the metal and other materials.
-
Will my home maintain its resale value?
Steel does not rot, nor does it have to be chemically treated like timber, and its strength over time is renowned. With these structural advantages your home will have an additional selling feature should you wish to sell it in the future. You’ll definitely want to tell the new owners about its advantages.
-
Will my home get a warranty?
It should, yes. That’s because most manufacturers belong to NASH and use AXXIS® steel for framing, which is produced by New Zealand Steel. New Zealand Steel provides a 50-year durability statement to meet the requirements of the NZ BC B2 Durability.
All components are precision manufactured computer-controlled roll formers and assembled to very tight tolerances. Because of the high thermal conductivity of steel and the thermal breaks it stays dry under all but exceptional weather circumstances. If water gets into the wall cavity it is not absorbed by the framing and so can readily evaporate.
-
Will a steel home look different than the rest in a housing development?
Only if it is meant to. With the strength of steel, architects and designers can create homes that have far larger open spaces than previously possible with antiquated building approaches.
Cladding finishes for steel framing can be the same as other homes and there is no restriction on the type of wall cladding. Bricks, weatherboard, and EIFS (External Insulation Finishing System) can all be used. Roof pitches can be low or high and roof claddings can be concrete, metal tiles, or profiled metal cladding. Whatever the choice, your finished home can fit in or stand out – the choice is yours.
-
What about the environmental impact of steel framing construction?
For delivering enduring, effective, and altogether exceptional outcomes, sustainable steel framing is extremely resilient and long-lasting, has a remarkably low carbon over the course of its lifespan, is adaptable (making for ease of retrofitting and re-use of existing structures), and can be used again and again.
-
Can mould grow on steel framing in houses?
Mould requires an organic nutrient source and moisture to grow. Kiln-dried Pinus timber has between 10-18% residual water content. This means that without chemical treatment it will rot and promote mould. Steel cannot promote the growth of mould because it is not absorbent.
-
What will happen to the steel framing should the house have to be demolished?
Any small amount of steel scrap has value and can be recycled. If for any reason your steel framed house must be demolished then it can be reused, relocated, or recycled. As steel is a valuable commodity it will not end up as landfill.
-
Is a steel frame house safe when exposed to a live electric wire?
Steel frames are safe because they are earthed.
-
Does CFS conduct sound through inter-tenancy walls?
Sound vibrations are conducted through any wall with solid material. Light Steel Framing is very slightly better at acoustic insulation than timber framing, due to the flange flexibility. However, the differences are only 1 or 2 decibels and not usually noticeable.
This means that a different wall design is used between apartments or flats. This can be one wall with several layers of gypsum linings plus sound insulating fiberglass or consist of two separate walls (with each insulated and disconnected from one another). Care must be taken when cutting penetrations into the inter-tenancy walls (e.g, for power, TV outlets, air-conditioning units etc) as these will provide a sound path.
-
Can I do an alteration that involves adding another storey with a steel framed house?
If the house was not initially designed for the extra storey then, in the same way as required with a timber house, foundations and walls have to be checked and may need to be strengthened. If you want to move load bearing walls it is wise to use an engineer who has experience with steel framing. The big advantage of a steel wall is that it can be disassembled and reassembled in position with just a screw gun. However, the amount of work required for this will be similar to that with a timber framed house.
-
Does the steel frame interfere with radio, phone, or TV signals?
No. Electromagnetic waves pass through the spaces between studs which allow the use of radios, phones, and television sets in a steel frame home without interference. The steel framing will provide marginally better protection from outside electromagnetic fields if you happen to live under a high voltage overheard power line.
The history of steel framing
-
How long has steel framing being around?
While steel framing has been available in New Zealand for over 50 years, the use of this construction material internationally had started far earlier.
There are a few speculative claims about who constructed the first building using Cold-Formed Steel (CFS). However, it’s known that use of CFS for construction of buildings started in both the United States and England in the 1850s. Use at this time was largely experimental and limited to a few basic structures.
During the 1849 California Gold Rush, New York roofer Peter Naylor advertised “portable iron houses for California”, with iron that was grooved so all parts could slide together. According to the ad, “20’ x 15’ homes could be built in less than a day, were cheaper than wood, fireproof, and more comfortable than a tent.”
Mr. Naylor used metal roofing in his practice in New York, so undoubtedly many of the components of these ‘iron houses’ were cold-formed steel. In the 1920s and 30s, acceptance of cold-formed steel as a construction material was limited. There was not an adequate design standard, and no information on the use of the material in the building codes.
That changed in 1933 when cold-formed steel made its official premiere at the World’s Fair in Chicago, where it was featured as a “home of the future”. Three houses were constructed in this exhibit area, and they all made significant use of cold-formed shapers or were entirely framed in steel.